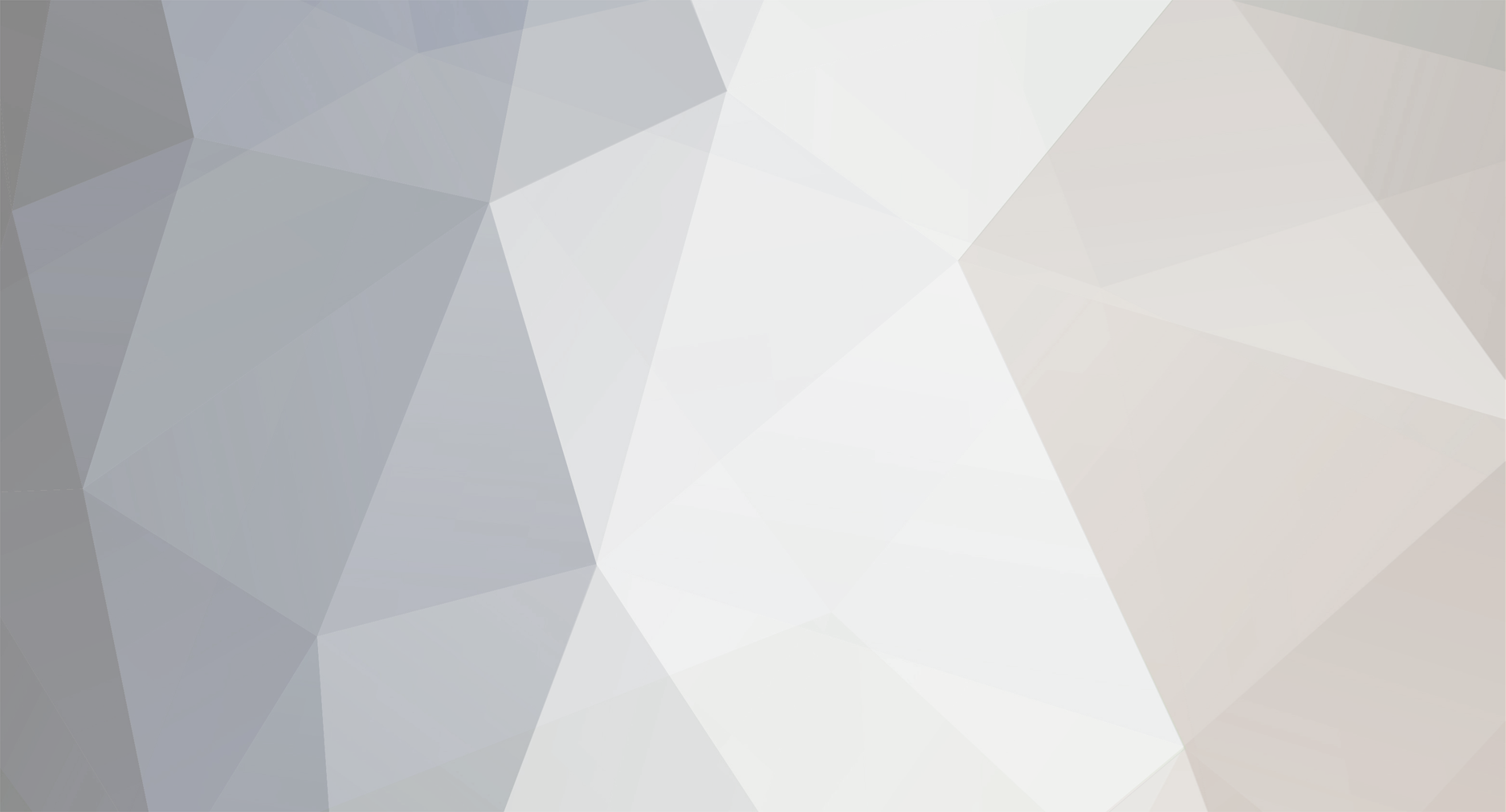
Caster
Banned-
Posts
9,318 -
Joined
-
Last visited
-
Days Won
84 -
Feedback
100%
Content Type
Forums
Events
Store
Articles
Everything posted by Caster
-
That cost money. I'll pass. :) I know a local guy who paints cars. He owes me a favor or two and he's gonna need a good set of used tires soon. He's probably gonna paint it...he just don't know it yet. He's one of one those guys that travels to car lots, setting up the tent to do touch ups and what not. He's on the look out for Toyota yellow. He has the paint code. He'll find some 'extra' left over from a job one of these days.
-
I am SERIOUSLY considering yellow. I think I would like to coat the whole thing in bedliner. Let that cure then pain the whole thing Tonka Yellow, then paint the roof white. Why you ask? Well, matching the tow vehicle would look pretty cool.....
-
Thank you for your service. Welcome, jump right in.
-
You were thinking bout assless chaps. Yep, that explains much.
-
Mark you brought up another good point. I can't beleive I actually thought of it already. Usually Im pretty slow. I cut the axle so that from outside to outside of the TIRES not the hubs or wheels, measure right at an inch less than my FJ. If my FJ will fit, the trailer HAS to. The ride height is level and the roof is about three inches shorter than my luggage rack on the Toyota. I kept it as big as I could and still be in the shadow of the intended pull vehicle.
-
Might be great for the cowboy who's suffering the gout.
-
The pings on my Gaydar were off the chart too.
-
HA!! The back window in the shop here at the tire store is an old glass storm door hung sideways. Tilt it up and prop it open in the summer, let it down in the winter. Save money on crap like that.......more money for powder, primers & bullets!!!!!!!!!!!
-
I was told by several people I got too carried away with my pintle. I used this because it was give to me I used 3x3x1/8" tubing for the tongue. I cut enough out the top and bottom of the tubing to beat this thing in with a hammer. Then tack welded it. Then I drilled both sides to open up those holes and drove two pieces of 1/2" coldrolled in there, beat them fuggers like a rivet, welded them, ground it smooth and then welded all the way around the thing. THEN, I used 1/8" thick steel tread plate and made two scabs like shown on my other joints. They extend back onto the tongue about 8 inches, top and bottom. I welded them to the tongue and while they were hot I beat them down to the contour of the angle leading up to the loop. THEN, I welded them in solid and even though it gave me a migraine I watched the puddle on the lunette. I was burning DEEP into it. I feel confident it will handle what I throw at it.
-
I use a 3/32 6011 rod to start and go over it with a 1/8 6011 rod. 70 amp to start and kick it to 90 for final welds. Really makes all traces of my first weld disappear AND makes sure all the voids and missed spots are gone.
-
Jesus wore sandals so maybe it's a Mormon thing? Tim Wilson said the book of mormon shoulda been called Jesus: The Western?
-
Actually....I'm working with what is FREE. In my mind, that's always the best design. So far, I have paid for the welding rods, spindles, hubs, leaf springs and a few nuts & bolts. I have a good buddy who does fab work all over middle TN. All the steel so far has been drops and scraps he has brought me. Thats the reason everything is built so heavy. It's worked out well too, welding 1/8" thick stuff is a JOY. No fear of burning through and I can really get a good solid weld.
-
Yep. I'm keeping it as balanced as I can for now because I known the toolbox will be heavy. Plus I don't know how the gear will balance out. Ideally, I want just heavy enough I have to grunt to set it on the pintle.
-
Pass I'm old and backwards. Slow and heavy penetrates. Penetration makes holes. Holes kill stuff.
-
You can get one from China cheaper.......
-
Oops, something went wrong, you're not permitted to see our online list. Not that I really care but funny I have the option to click "see full list" but am not allowed to see the full list. Ya'll trying to hide sumthin. I know you are. Can't lie to me. I knows it!
-
I am SERIOUSLY considering a water tank in the space between the axle and frame. I want the trailer finished first so I will know the final ride height and can get my shocks in place. But I figure I can get a 20-25 gallon square tank in there with steel bands like a gas tank. Then plumb it to trapdoor with a filler neck and use a solar powered 12v pump to get it out. The tool box up front will house a deep cycle marine battery and I will make a bracket for a solar panel on the roof. Bottle opener will be in the tool box if you need it. :up:
-
HiPower, the whole size of the trailer was designed around that top. That's the reason for the size. Peejman, the balance of it "Right Now" is such that I can lift the trailer with two fingers. I've kept that VERY much in mind. I'm banking on that tool box full of gear to MAKE it tongue heavy. You obviously don't want lots of tongue weight but it does need more up front so the lunette doesn't bounce going down the road. I will adjust the actual payload in the trailer accordingly.
-
http://www.tngunowners.com/forums/topic/88825-my-expedition-trailer-project/#entry1280137 I started a build thread for the whole trailer so ya'll can follow my halfassed work. :rofl: :rofl: :rofl:
-
Future plans are a tool box for the tongue.....but them things are EXPENSIVE!! Gotta box it in and I will probably buy a door for an RV for the back. They make some very neat frame/door units for tear drop campers or storage access doors for large RV's. This should handle enough gear for me and the woman to get the hell outta here in a hurry or just enjoy a weekend at the lake. The whole thing will get coated with bedliner when it's done. Then I'll paint the roof top white to shed heat.
-
My welding ain't so good. I have very light sensitive eyes and cannot watch my puddle like I need to. SO, I weld everything twice with the second weld penetrating the first. Decided to go with a pintle and lunette instead of a ball to give me more articulation. Used 2x2x 1/8" angle to make the body skeleton. Then used the aluminum roof from a M151A2 military jeep as a roof. I also got me some mud grip 265-70-17's and some aluminum toyota wheels. They aren't an exact match to my FJ but they're close. If you notice the door on the tongue, there's going to be a control panel in there to handle electrical. I'll likely have this thing lit up like a christmas tree. Redneck and all, I do love me some lights.
-
I'm not interested in ever doing repairs on this thing SO, I used 1/8" tread plate to make scab plates over critical joints. I welded everything together first, ground it smooth and welded plates over the joints.
-
I wanted an enclosed trailer that was offroad capable. God knows you ain't gettin' nowhere with a standard trailer once you leave the pavement. Life started with some 1/4 thick wall steel tubing and some spindles I got from Ebay. I wanted a 6 lug pattern so I can run a 265-70-17 on Toyota wheels. This way I have interchangeability with my FJ. Carry a spare for the trailer plus the one on the FJ and I have two spares for either. Check out the trash barrel and plywood I have for a work bench. Before anyone criticizes my shoddy workmanship, consider I have precisely SQUAT to work with here. I Lincoln stick welder, a right angle grinder and cut off wheels. That's about it other than a hammer and a give 'em hell attitude. :rofl: Then I framed up the trailer using 1/8" thick square and rectangle tubing. 3" square and 2x5" rectangle. I used a set of Ford F150 leaf springs with the overload leaves removed. Once the trailer is done I have made some perches and will weld them in for a set of Monroe shocks. I also drilled & cross drilled the shackle bolts for grease fittings so I can grease those joints. I turned some cold rolled steel in my lathe and made inserts that go through the square tubing for the bolts and welded them in, so the bolts aren't riding in just the tubing, but have a full length surface to bear on. They're exponentially stronger that way and will prevent wear long as I keep them greased.
-
Thanks MacGyver. I have a bucket of latex sealer I thought about sealing the whole sheet but I think that would be counterproductive. Like you pointed out, it makes more sense [now thinking about it] to allow the plywood to breath on the inside. Thanks to everyone. I really need to get back to this little project and get it done.